How to achieve consistent product quality on a production line with digital solutions
January 22, 2025
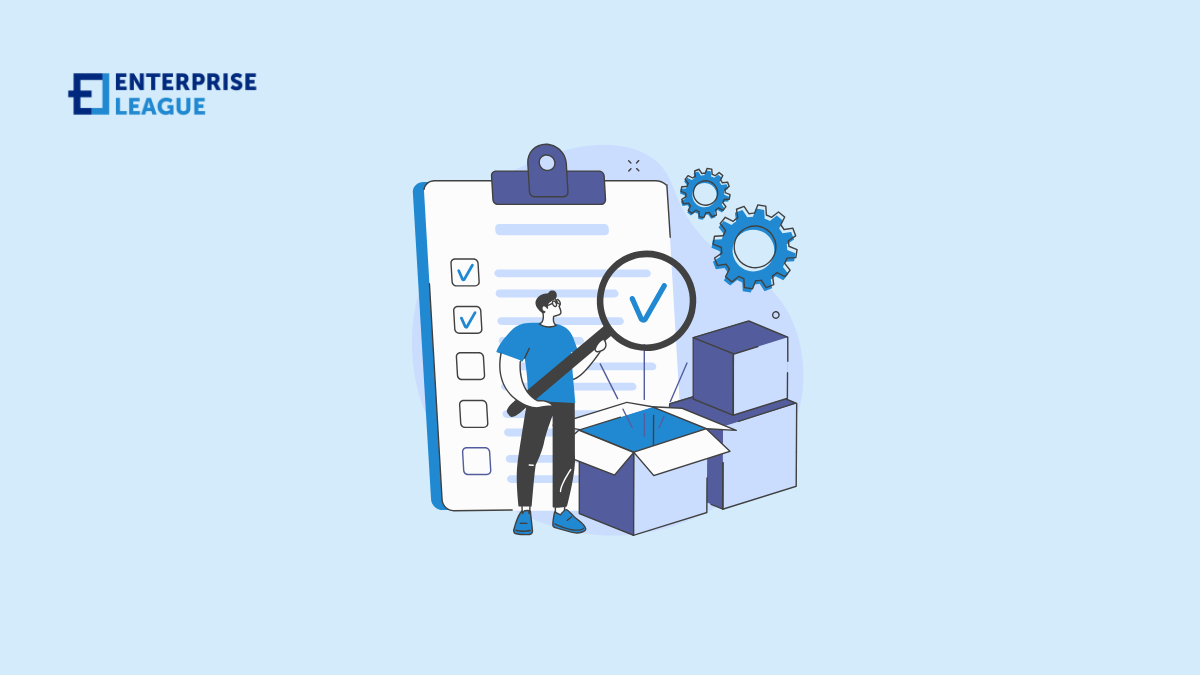
Quality control in manufacturing used to be a game of catch-up – finding problems after they’ve already happened. But digital solutions are flipping that story on its head. Now, manufacturers can spot and solve issues in real time, predict problems before they occur, and keep production running at peak quality.
From automated inspections to data-driven decisions, these tools are helping companies deliver better products more consistently.
Implementing a comprehensive quality management system
Quality control in manufacturing has come a long way from clipboards and checklists. A robust Quality Management System (QMS) acts like your factory’s brain, connecting every process and person involved in making your products great. Digital QMS solutions are changing the game by turning mountains of quality data into actionable insights you can use right away. Let’s break down some of the key benefits of a digital QMS:
- One source of truth for all quality documents
- Instant alerts when quality slips
- Clear visibility into supplier reliability
- Better team training tracking
- Automated compliance reporting
- Smart insights for constant improvement
Making the switch to digital quality management means preparing your business for the next wave of manufacturing innovation. When quality becomes automatic, you can focus on what really matters and that is growing your business and staying ahead of the competition.
Leveraging IoT for real-time quality monitoring
Think of IoT as your quality control team that never sleeps. While traditional quality checks happen at specific points, IoT-powered systems watch every step of production around the clock. By plugging sensors, cameras, and tracking devices into your manufacturing line, you create a digital nervous system that feels every hiccup in your process. What makes IoT quality control different is:
- Sensors that spot tiny changes before they cause big problems
- Smart cameras that check every product, not just random samples
- Digital tracking that tells you where everything is, all the time
- Connected systems that share information instantly
The real power kicks in when all these tools work together. Your machines can tell you when they need maintenance before they break down. Your cameras can spot defects faster than any human inspector. And your tracking system knows exactly where to find that one batch that might have issues. It’s like giving your factory a sixth sense of quality, the one that helps you make better products while spending less time and money on fixes.
The power of big data analytics
Big data is changing the game for quality control in manufacturing. Imagine having a system that not only tracks every detail of your production but actually learns from it, getting smarter every day. That’s what big data analytics brings to the factory floor, turning information overload into your biggest quality control advantage. What sets big data quality control apart is:
- Learns from every product you make
- Shows you where money is being wasted
- Helps you design products that last longer
- Turns production data into profit opportunities
- Makes quality control decisions based on facts, not hunches
- Keeps your whole team on the same quality page
When your quality control system can learn from millions of data points, you’re not just fixing today’s problems, you’re preventing tomorrow’s headaches. The result? Less waste, fewer returns, happier customers, and a healthier bottom line. That’s the real power of putting your data to work.
Implementing statistical process control (SPC)
Statistical Process Control or SPC has become more powerful with each technological advance, helping manufacturers spot and fix quality issues faster than ever before. Today’s SPC tools do more than just crunch numbers, they give you a crystal-clear view of your entire production process, showing you exactly where and when quality might slip. Some of the key features that make a difference are:
- Real-time process monitoring that never sleeps
- Automated analysis that flags potential problems
- Smart sampling that saves time and resources
- Trend detection that helps prevent future issues
Put these tools to work, and you’ll spend less time-fighting fires and more time improving your products. When every person on your production floor has access to clear, actionable quality data, maintaining high standards becomes part of your daily routine rather than a constant struggle.
Empowering employees through digital training and collaboration
Even with all the latest quality control tech, it’s still people who make the real difference. That’s why smart manufacturers are using digital tools like e-learning platforms, AR guidance, and collaborative software to help their teams work better and smarter.
These tools don’t replace human expertise, they enhance it, giving employees instant access to training, real-time guidance, and shared knowledge. When people and technology work together like this, maintaining high-quality standards becomes a natural part of everyone’s day.
Implementing automated visual inspection systems
While human inspectors can get tired or distracted, these AI-powered systems keep their digital eyes on every product that rolls off your line, using advanced cameras and smart algorithms to catch things the human eye might miss.
They’re not just taking pictures, they’re building a detailed 3D understanding of your products, measuring and analyzing at speeds that would make your head spin. Plus, all that inspection data feeds right back into your production system, helping you spot and fix problems before they become costly mistakes.
Predictive maintenance for quality assurance
Using smart sensors and data analysis, it spots potential equipment problems before they affect your product quality. Instead of waiting for machines to break down or produce defects, these systems tell you exactly when and what maintenance is needed.
By keeping your equipment healthy, you’re not just preventing downtime, you’re ensuring consistent quality, reducing waste, and saving money on repairs and rework. When your machines run better, your products come out better, it’s that simple.
Implementing digital twin technology for process optimization
Using smart sensors and data analysis, it spots potential equipment problems before they affect your product quality. Instead of waiting for machines to break down or produce defects, these systems tell you exactly when and what maintenance is needed.
By keeping your equipment healthy, you’re not just preventing downtime, you’re ensuring consistent quality, reducing waste, and saving money on repairs and rework. When your machines run better, your products come out better, it’s that simple.
Conclusion
The key to success lies in integrating these various digital solutions into a cohesive quality control strategy. Quality control software for manufacturing, such as the solutions offered by LineView, can serve as the central platform for managing and optimizing these diverse quality control initiatives.
More must-read stories from Enterprise League:
- How to handle a situation where employees are not getting along.
- Creative spiritual business ideas that you can start today.
- How to ask for a deposit in a contract without being awkward or losing a client.
- Have a look at the best countries to start a business as a foreigner.
- All the reasons why we should support local businesses and shop local.
Related Articles
How Digital Transformation Optimizes Your Expenses and Other Resources
Nowadays, it is a real challenge to find a successful business that hasn't implemented digital transformation. The variety of available software solutions and services, such as ready-made business management platforms or custom business software development on demand,...
Who Sells Automotive Lifts With Nationwide Installation and Service Coverage
Business owners must equip their shops and employees with reliable equipment. However, sourcing the right tools for the job may be challenging if you don't have suppliers nearby. It's best to rely on industry professionals with established networks and service...
What Makes Resume Writing Services Worth the Price
A polished resume often stands between a job seeker and their next opportunity. With hiring managers spending just seconds on each application, every line and layout choice counts. For many professionals, hiring a resume writer is a strategic investment in their...
How Digital Transformation Optimizes Your Expenses and Other Resources
Nowadays, it is a real challenge to find a successful business that hasn't implemented digital transformation. The variety of available software solutions and services, such as ready-made business management platforms or custom business software development on demand,...
Who Sells Automotive Lifts With Nationwide Installation and Service Coverage
Business owners must equip their shops and employees with reliable equipment. However, sourcing the right tools for the job may be challenging if you don't have suppliers nearby. It's best to rely on industry professionals with established networks and service...