Ensuring quality and safety: Best practices in medical equipment manufacturing
April 12, 2023
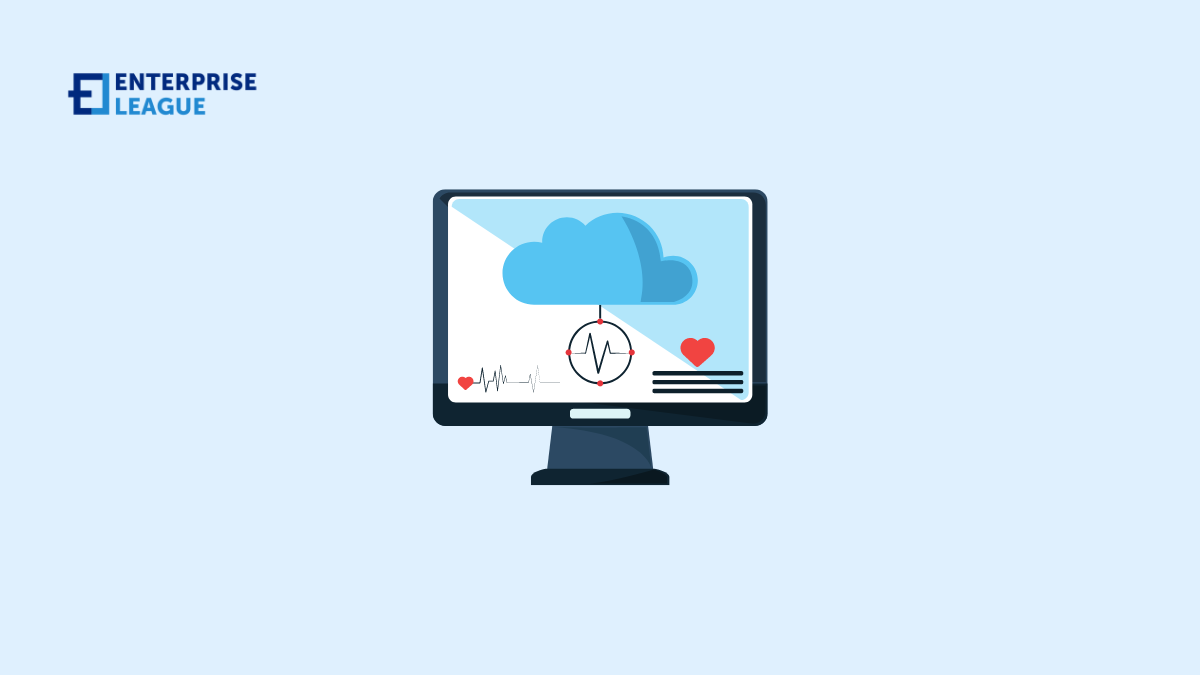
This article covers the most effective practices in medical equipment manufacturing that assure the creation of dependable and secure equipment.
7 best practices for consistent and efficient medical equipment manufacturing
To achieve consistent and efficient manufacturing processes that comply with established standards, implementing quality practices is crucial. To prevent defects and errors during production that could lead to costly recalls and damage to the manufacturer’s reputation, following the best practices is essential.
Below is a checklist of seven best practices that must be followed during medical equipment manufacturing.
Create a plan
Creating a plan is essential for efficient medical equipment manufacturing because it provides a structured approach to the production process. A well-designed plan allows manufacturers to identify potential challenges, establish clear objectives, allocate resources effectively, and track progress toward the set goals.
By having a plan, medical equipment manufacturers can reduce errors, minimize downtime, and optimize their manufacturing processes, resulting in increased productivity and efficiency. Furthermore, having a plan can help manufacturers make informed decisions regarding best design of medical devices, raw materials, and personnel, ensuring that the manufacturing process adheres to established quality standards.
Understand the regulatory guidelines and standards
Medical equipment manufacturers should follow regulatory standards and guidelines from design to delivery. These involve quality management systems, process methods, labeling, and reporting. They should have processes focusing on inspection and product deficiency correction. Also, documentation is a requirement when manufacturing medical equipment to identify defects and incorrect procedures so they can be easily rectified in the future.
Choose high-quality materials
Using premium-quality materials is crucial in achieving the goal of manufacturing high-quality products that every manufacturer strives for. While design planning is among the most crucial steps in manufacturing medical equipment, you should also evaluate the raw materials used for the products.
You can choose the right materials by determining their durability, usability, and safety. Also, you should define the materials’ origins, sources, and manufacturing methods, among other things. This is especially important if you’re advocating for sustainability and want to ensure that every step of the process generates the lowest emissions possible.
Quality managers evaluate the technology and materials suitable for producing highly functional medical devices. The goal is to maintain the production rate while improving quality using better materials and methods.
Consider the product costs and target market
Other factors you need to consider are product costs and price sensitivity. A skimpy understanding of such areas can lead to a decline in medical equipment production and thus, incur losses.
Evaluating your target market not only helps you understand the client and patient needs but also increases your sales volume. Market research can help determine customer needs and optimal pricing in a competitive business arena. It’s even more beneficial if you sell equipment similar to your competitors. This way, you can develop unique features to make your products stand out.
Use proven practices
It’s best to utilize tested and proven processes rather than new ones. By following proven practices, manufacturers can ensure that their products are consistently high in quality.
Proven practices help manufacturers develop equipment that meets the necessary safety and efficacy standards. They can help reduce costs by optimizing production processes, reducing waste, and minimizing errors. This approach makes medical equipment more affordable and accessible to patients and healthcare providers.
Use feedback to improve product quality
A successful medical device manufacturing company embraces feedback from its clients. This includes feedback from medical providers and patients on how the products were received in the market, their effectiveness, and their benefits. That way, the manufacturer becomes aware of areas where improvements need to be made and learns more about its target customers.
In addition, the FDA requires medical device audits, which are part of the quality management process. Besides being necessary to the regulatory board, you can use internal audits to improve your products by identifying and refining the smallest concerns.
Be creative
There’s not one best procedure for manufacturing medical equipment. Furthermore, the medical market has a massive variety of uniquely designed products. This allows you to think outside the box and use your creative skills to develop new designs. New assembly methods and processes are a few examples of how you can try to innovate medical equipment.
Implementing the abovementioned practices will keep product flaws at bay and lawsuits due to defective equipment.
Conclusion
Following the practices for consistent and efficient medical equipment manufacturing can lead to improved quality, safety, and efficacy of medical equipment while also reducing costs and ensuring compliance with regulations and standards. However, manufacturers must follow the practices set under industrial guidelines to maintain relevancy in the market.
The seven best practices listed in this article will help you produce high-quality and functional products for your target market and customer needs.
More must-read stories from Enterprise League:
- Innovative small business growth tips that will take you to the next level.
- B2B payment solutions that can help you transform your business.
- Aspects that show the importance of cross-cultural communication in the workplace.
- What it takes to start a wholesale business from scratch?
- Find out how to turn your hobby into a business.
Related Articles
What Are the Top-Rated Waste Management Software Solutions?
Managing waste efficiently has become critical for businesses focused on sustainability and environmental responsibility. Companies of all sizes now rely on specialized technology to improve accuracy, compliance and efficiency in their waste operations. Software...
Leadership Strategies for Post-Rehab Reintegration: How to Support Employees Returning from Residential Rehab
When an employee returns to work after completing an alcohol rehab or residential rehab program, it represents an important step in their recovery and a critical moment for your organization. As a leader, your actions can either strengthen their commitment to...
What do you need to qualify for credit card debt consolidation?
Managing multiple credit card payments can be overwhelming, especially when high interest rates keep your balances from shrinking. Credit card debt consolidation through a personal loan might help simplify your finances and reduce interest costs - but qualifying isn't...
What Are the Top-Rated Waste Management Software Solutions?
Managing waste efficiently has become critical for businesses focused on sustainability and environmental responsibility. Companies of all sizes now rely on specialized technology to improve accuracy, compliance and efficiency in their waste operations. Software...
Leadership Strategies for Post-Rehab Reintegration: How to Support Employees Returning from Residential Rehab
When an employee returns to work after completing an alcohol rehab or residential rehab program, it represents an important step in their recovery and a critical moment for your organization. As a leader, your actions can either strengthen their commitment to...