4 Tips for integrating robotic polishing into your business operations
October 05, 2023
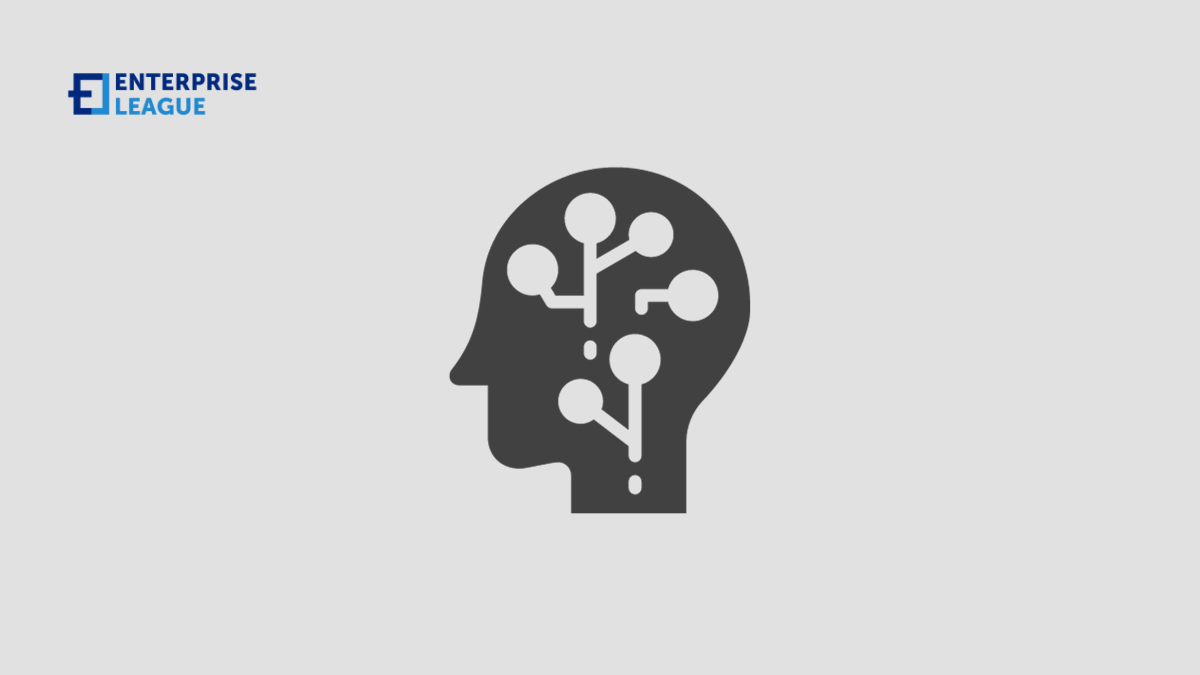
The reality of robotic polishing is upon us, and many businesses can benefit from weaving it into the fabric of their existing operations and processes.
Of course this is easier said than done, and there are a number of potential hiccups and obstacles that have to be encompassed in your plans early on.
To grease the wheels of robotic polishing implementation, here are some tips to guide you as you get started.
Evaluating your business needs for robot integration
Incorporating robotic polishing into your operation isn’t a decision made lightly. There are many factors to consider, including the size of your production line, workforce capabilities, and long-term financial prospects. Here’s what you should take in mind:
- Production Requirements: Evaluate if automation will increase efficiency and reduce overall operational costs.
- Workforce Adaptability: Understand the potential impact on employees as they may need training to operate the new system.
- Financial Considerations: Determine whether this is financially sustainable. Explore both initial expenses for purchasing and installation as well as long-term savings it could provide.
In short, successful integration begins with making an informed decision, so conduct extensive research and consider every aspect relevant to your business scenario before moving forward.
Selecting the ideal robotics polishing system for your operations
Once you’ve determined your business needs, it’s time to choose a robotic system that fits them. Here are some pointers to consider when making this critical decision:
- Functionality: Ensure the selected robot has capabilities matching your specific industry, operational requirements, and production plans.
- Reliability and Durability: Prioritize systems by renowned manufacturers with warranty coverage; they should also be able to handle extensive usage without breakdowns.
- Supplier Support: Choose suppliers who offer in-depth technical support and maintenance services post-purchase.
Moreover, consulting an expert on robotics could help guide you towards finding an optimal solution tailored for your specific needs, aiding in smoother integration of the system into your operations.
Creating optimal workspaces
Proper setup is crucial for a safe, efficient robotic work area. Here are essential guidelines:
- Designated Space: Assign specific areas for the robot to avoid clutter and ensure smoother operation.
- Safety Precautions: Implement safety measures like safety interlocks or emergency stops. Create boundaries with either physical structures or light curtains to keep human operators safe.
- Noise Reduction: Since automated systems can be noisy, strategize noise reduction techniques as well to adhere to government regulations.
The idea is to create an environment that works for both staff and machines, without cutting corners. This approach will lead to not only increased productivity but also enhanced worker satisfaction within a secure workspace.
Training staff and managing change effectively
Incorporating robotics means change, which might invite resistance from your employees. Therefore, clear communication and employee training become key to successful integration:
- Open Conversations: Talk about the benefits of robotic systems to dispel any fears or misconceptions.
- Appropriate Training: Provide comprehensive training sessions for staff so they can safely operate and maintain the new system.
- Supportive Environment: Offer help when required along with regular performance reviews as it aids in maintaining job satisfaction while making them comfortable with technology.
Effectively managing change is a crucial part of smooth robotics integration into business operations. It’s critical that personnel feel supported during this transition.
Conclusion
The last point to keep in mind is that your responsibilities don’t end once your robotic polishing infrastructure is up and running. You have to be ready to analyze its performance, carry out preventive maintenance, and think about eventual upgrades so that you aren’t caught out by any surprises in the weeks, months and years that follow.
More must-read stories from Enterprise League:
- Key factors in determining salary increases for your employees.
- How to handle a situation where employees are not getting along.
- A step-by-step guide to teach you how to write a business essay.
- Smart ways to enhance the efficiency of your business.
- Profitable and funny business idea that you can start today.
Related Articles
How to turn your hobby into a business in 2024
How long have you been dreaming to turn a hobby into a business and swim in cash? Stop dreaming, read our article and take action.
Home office security: 10 cybersecurity tips for remote workers
Working from home has become a reality and there are new challenges associated with remote work and maintaining the security of sensitive information.
6 supply chain challenges and how to solve them
When your business works with physical products it won’t be long until certain supply chain challenges arise. Knowing how to deal with these supply chain issues is crucial.
How to turn your hobby into a business in 2024
How long have you been dreaming to turn a hobby into a business and swim in cash? Stop dreaming, read our article and take action.
Home office security: 10 cybersecurity tips for remote workers
Working from home has become a reality and there are new challenges associated with remote work and maintaining the security of sensitive information.